The main difference between axial and centrifugal fans lies in their design and performance characteristics. Axial fans move air parallel to their rotating shaft, offering high airflow with low pressure, while centrifugal fans draw air into the center and discharge it radially, generating higher pressures.
Axial fans are typically more compact and energy-efficient, suitable for electronics cooling and HVAC systems, whereas centrifugal fans excel in industrial applications and handling particulate-laden air.
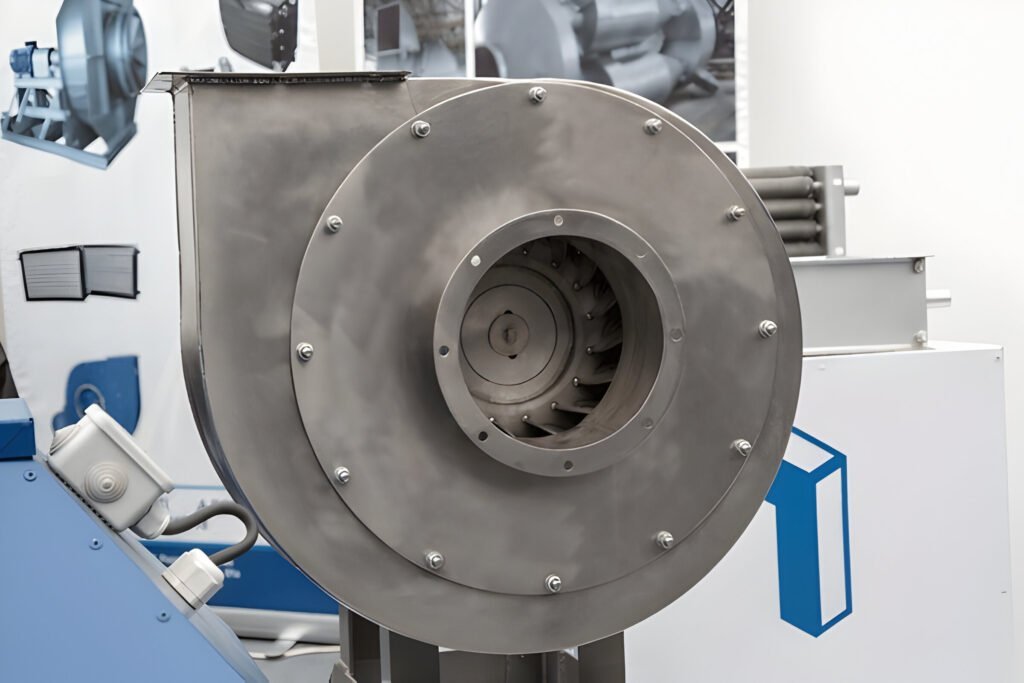
What Are Centrifugal Fans
Centrifugal fans also know as centrifugal blower fans, draw air into the center of a rotating impeller and discharge it radially outward. This design generates higher pressures and handles challenging airflow conditions.
The main components of centrifugal fans are a wheel or impeller with blades mounted around its circumference. The spinning impeller creates centrifugal force, propelling air outward. The fan housing directs this air to the desired outlet.
Centrifugal fans excel at moving air against high static pressures, making them ideal for systems with complex ductwork or long-distance air movement. They effectively handle particulate-laden air, as the centrifugal action separates particles from the airstream. While bulkier and more power-consuming than axial fans, centrifugal fans offer superior performance in high-pressure applications and can be more energy-efficient for certain tasks.
How Centrifugal Fans Work
Centrifugal fans utilize rotating impellers to draw air into their center and expel it radially outward. The spinning impeller creates centrifugal force, pushing air towards the fan housing’s outer edges. This action increases air velocity and pressure, overcoming system resistance.
The fan’s scroll or volute-shaped housing directs airflow, collecting and guiding air discharged from the impeller. This design produces a steady, high-pressure airstream.
Applications for Centrifugal Fans
HVAC Systems and Building Applications
HVAC systems utilize these fans for air conditioning, ventilation, and heating in buildings. Their ability to move large air volumes against high pressures makes them suitable for complex ductwork systems.
Industrial Uses
Industrial settings employ centrifugal fans for dust collection, fume extraction, and material handling. Cement plants, steel mills, and woodworking facilities use them to remove airborne particles. Automotive applications include vehicle cooling systems and turbochargers.
Power Generation and Mining
Power plants incorporate centrifugal fans in cooling towers and forced draft applications. The mining industry relies on these fans for ventilation in underground shafts and tunnels. Agricultural uses encompass grain drying and crop aeration.
Clean Room and Specialized Applications
Clean rooms in pharmaceutical manufacturing and semiconductor production depend on centrifugal fans to maintain air quality. These fans also find applications in commercial kitchen exhaust systems, wastewater treatment plants, and some vacuum cleaners.

What Are Axial Fans
Axial fans move air parallel to their rotating shaft using propeller-like blades. Their design ranges from small computer cooling fans to large industrial ventilation systems. The straightforward construction features blades arranged within a cylindrical casing, creating a pressure difference to propel air. This configuration allows high airflow rates but generally produces lower pressure than centrifugal fans.
These fans excel in applications requiring large air volume movement with low pressure needs. They operate efficiently in open spaces, making them suitable for ventilation, cooling, and exhaust systems. Common uses include computer hardware, automotive radiators, and HVAC systems. Axial fans also find applications in wind tunnels, cooling towers, and jet engines.
How Axial Fans Work
Axial fans operate by moving air parallel to their rotating shaft, creating axial flow. The spinning blades generate a pressure difference between the fan’s inlet and outlet sides. A typical axial fan consists of a cylindrical housing, a rotor with multiple blades, and a motor.
The motor turns the rotor, causing the blades to cut through the air and push it forward. Most axial fans employ airfoil-shaped blades to maximize air movement while reducing turbulence.
Blade rotation creates a low-pressure area in front of the fan and a high-pressure area behind it. This pressure differential forces air through the fan.
Applications for Axial Fans
HVAC and Electronics Cooling
HVAC systems employ axial fans for building ventilation and air circulation. Computers and electronics use axial fans to cool components and prevent overheating.
Automotive and Industrial Applications
The automotive industry integrates axial fans into engine cooling systems and air conditioning units. Power plants utilize them in cooling towers, while wind tunnels incorporate them for aerodynamic testing. Large-scale air-moving applications, such as mine and tunnel ventilation systems, rely on axial fans.
Agricultural and Marine Uses
Agriculture benefits from axial fans in crop drying and livestock ventilation processes. The marine industry uses them for engine room ventilation and cargo hold air circulation. Industrial processes implement axial fans in drying, cooling, and exhaust systems. Personal comfort devices like floor and ceiling fans also employ axial technology.
Aerospace and Safety Systems
Aerospace applications include aircraft environmental control systems. Fire safety systems use axial fans for smoke extraction. Small appliances such as hair dryers and vacuum cleaners incorporate axial fan technology for air movement.
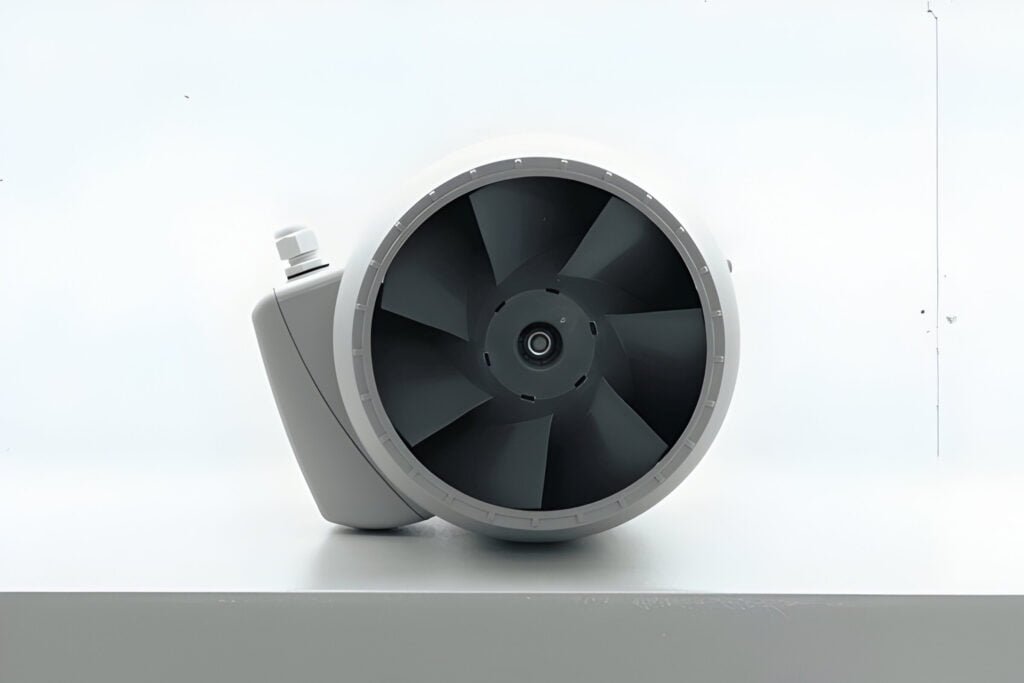
What Are the Similarities Between Centrifugal and Axial Fans
Centrifugal and axial fans share key similarities despite their design differences. Both types move air or gases between locations, serving as vital components in HVAC systems, industrial processes, and electronics cooling.
Rotating blades create airflow in both centrifugal and axial fans. They convert mechanical energy from electric motors into kinetic energy in the air stream.
What Are the Difference Between Centrifugal and Axial Fans
Blade Angle
Axial fans feature fixed-angle blades relative to the rotation axis, determining airflow and pressure performance. Many axial fans offer adjustable blade angles for application-specific optimization.In axial fans, steeper angles produce higher pressure but lower airflow, while shallower angles yield higher airflow at lower pressures.
Centrifugal fans use curved or angled blades in relation to the radial direction. The blade angle impacts air exit velocity and pressure. Centrifugal fan designs include forward-curved, backward-curved, and radial blades. Centrifugal fans with backward-curved blades offer improved efficiency and stability. Forward-curved blades provide increased airflow at lower pressures.
Size and Installation
Axial fans offer compact, streamlined designs suitable for space-constrained applications. They move air parallel to their shaft, enabling in-line duct mounting in HVAC systems. This feature makes them easier to install in tight spaces.
Centrifugal fans require more installation space due to their larger size. They change airflow direction by 90 degrees, necessitating clearance for both inlet and outlet. This design often requires complex mounting setups and additional ductwork or housing.
Noise Levels
Axial fans produce more noise, particularly at high speeds, due to their blade design and airflow pattern creating turbulence.
Centrifugal fans operate more quietly, making them suitable for noise-sensitive applications. Their enclosed design and air movement method contribute to reduced noise output.
Cost
Axial fans typically cost less than centrifugal fans for comparable air flow rates due to their simpler design and fewer components. This price difference reflects in the initial purchase price, favoring axial fans.
Centrifugal fans often exhibit higher energy efficiency, potentially leading to lower operating costs over time, especially in high-usage scenarios.
Airflow Direction and Pressure Characteristics
Axial fans move air parallel to the rotation axis, entering and exiting in a straight line. This design enables high airflow rates but lower pressure capabilities, making them suitable for applications requiring large air volumes with minimal resistance.
Centrifugal fans change airflow direction by 90 degrees. Air enters parallel to the rotation axis and exits perpendicular to it. This redirection results in higher pressure capabilities compared to axial fans. Centrifugal fans excel in systems with significant airflow resistance or high-pressure requirements.
Durability
Centrifugal fans offer superior durability compared to axial fans due to their robust construction and enclosed design. The impeller blades in centrifugal fans are less exposed to the environment, reducing damage risk from debris or contaminants. This design allows them to handle higher temperatures and abrasive materials with minimal wear.
Axial fans, while less durable, provide reliable performance in many applications. Their open blade design makes them more susceptible to damage from foreign objects. However, this simplicity often results in easier cleaning and maintenance.
Power Consumption
Axial fans consume less power than centrifugal fans in low-pressure applications. Their straight-line airflow design requires less energy, resulting in lower operational costs. Centrifugal fans become more efficient in high-pressure scenarios, despite higher initial power consumption. They maintain efficiency when overcoming system resistance, making them suitable for applications with long ductwork or extensive air filtering.
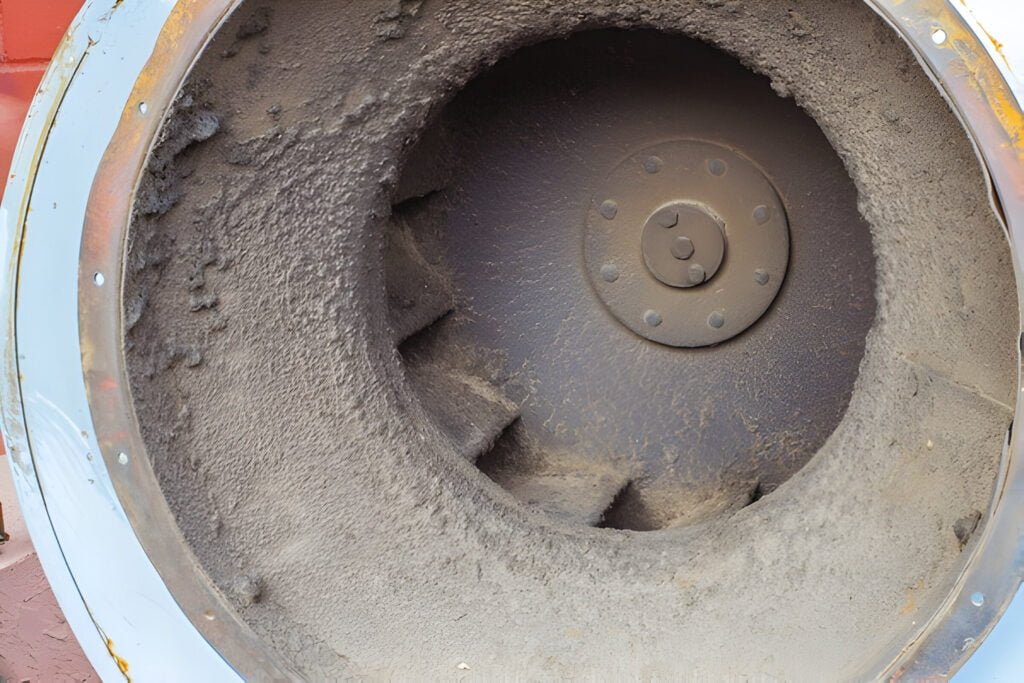
Factors to Consider When Selecting Between Axial and Centrifugal Fans
Airflow Volume and Pressure Requirements of the Application
Airflow volume and pressure requirements dictate the choice between axial and centrifugal fans. Axial fans move large air volumes at low pressures, suiting ventilation systems and cooling towers. They efficiently transport air across open spaces with minimal resistance.
Centrifugal fans handle higher pressures and lower airflow rates, excelling in systems with ductwork or obstructions. These fans perform well in industrial processes, material handling, and HVAC systems with extensive ductwork.
System-specific pressure and flow requirements determine fan selection. Axial fans operate in the 0-2 inches of water gauge (in. wg) static pressure range, moving up to 500,000 cubic feet per minute (CFM). Centrifugal fans manage pressures up to 20 in. wg or higher, handling airflow volumes up to 100,000 CFM.
Space Constraints and Noise Considerations
Space constraints and noise levels influence fan selection. Axial fans offer compact designs, ideal for limited installation spaces in computer cooling systems or automotive radiators. Centrifugal fans, while larger, accommodate various housing shapes to fit specific space requirements, often used in HVAC systems within ductwork or ceiling spaces.
Noise considerations affect fan choice. Axial fans produce higher noise levels, especially at higher speeds, due to blade design and airflow patterns. This can be problematic in noise-sensitive environments like offices or residential areas. Centrifugal fans operate more quietly, with better noise absorption within the housing, making them suitable for applications requiring low noise levels.
Energy Efficiency Needs
Axial fans provide higher efficiency at lower pressures and higher flow rates, making them ideal for applications requiring large air volumes with minimal resistance. Cooling towers, ventilation systems, and heat exchangers commonly use axial fans.
Centrifugal fans excel in high-pressure, lower flow rate scenarios. They operate more efficiently in systems with extensive ductwork or substantial pressure drops. HVAC systems, industrial processes, and material handling applications typically employ centrifugal fans.
Upfront Cost Vs Long-Term Performance and Durability
Axial fans offer lower initial costs due to simpler design and fewer components. Their ease of manufacture and installation makes them attractive for budget-conscious projects. Centrifugal fans provide better long-term value despite higher upfront expenses. Their robust construction and ability to handle harsh conditions result in longer lifespans and fewer replacements.
Centrifugal fans maintain efficiency better as they age, delivering consistent performance and energy savings throughout their operational life. This durability can justify the higher initial investment, especially in demanding industrial applications or situations where downtime is costly.
FAQs
Can Axial and Centrifugal Fans Be Used in Series or Parallel?
Axial and centrifugal fans can be used in series or parallel configurations. Series arrangements increase pressure, while parallel setups enhance airflow.
How Do Axial and Centrifugal Fans Perform in High-Temperature Environments?
Centrifugal fans excel in high-temperature environments, offering superior efficiency and heat tolerance. Axial fans, while functional, may experience reduced performance and efficiency when exposed to extreme heat conditions.