In the realm of electric motors, two prominent contenders often take center stage: induction motors and DC brushless motors. While both serve the purpose of converting electrical energy into mechanical motion, they employ distinct principles and exhibit unique characteristics that set them apart.
This blog post aims to delve into the intricacies of induction and DC brushless motors, shedding light on their operating principles.
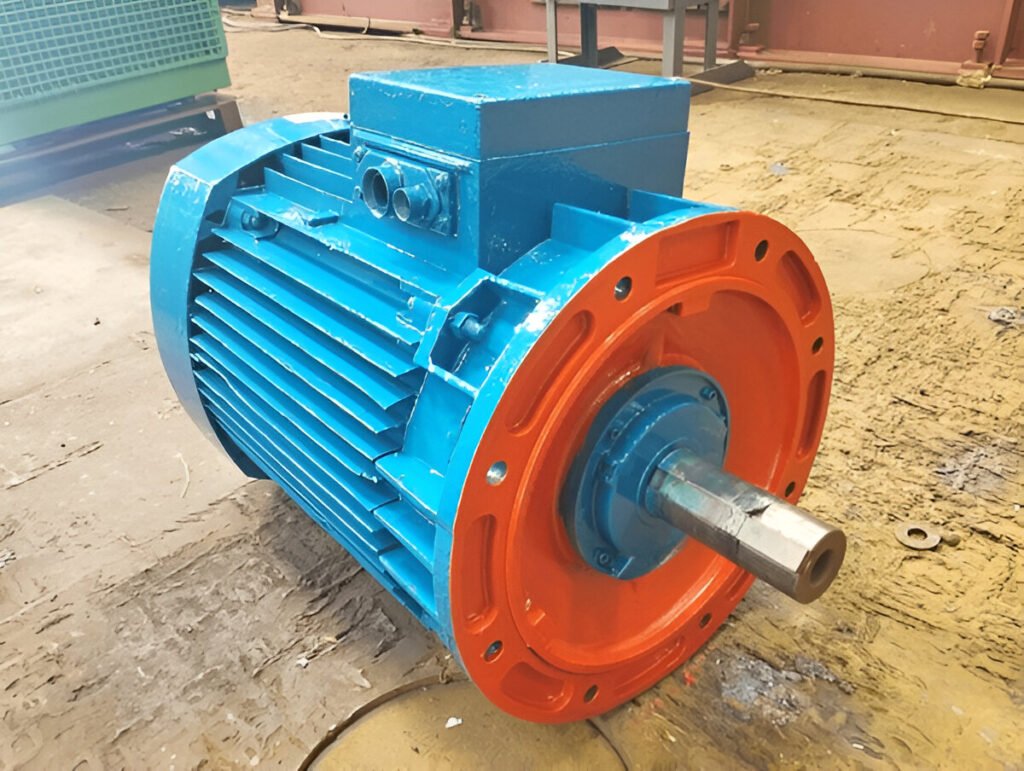
What Is Induction Motor
An induction motor, also known as an asynchronous motor, is an AC electric motor that converts electrical energy into mechanical energy through electromagnetic induction. It is the most widely used type of motor in industrial applications due to its simplicity, durability, and low cost.
The main components of an induction motor include:
- Stator: The stationary part of the motor, consisting of a cylindrical core with windings that produce a rotating magnetic field when energized with AC current.
- Rotor: The rotating part of the motor, typically made of a laminated core with conducting bars or windings arranged in a cylindrical shape.
- Bearings: Support the rotor and allow it to rotate freely within the stator.
- Frame: Houses and supports the stator, rotor, and bearings.
How Induction Motors Work
Induction motors operate on the principle of electromagnetic induction, converting electrical energy into mechanical energy. The motor consists of two main components: a stationary stator and a rotating rotor. The stator contains windings that create a rotating magnetic field when energized with alternating current (AC). This rotating magnetic field induces currents in the rotor’s conductive bars.
The induced currents in the rotor interact with the stator’s magnetic field, generating a torque that causes the rotor to spin. The rotor always rotates at a slightly slower speed than the rotating magnetic field, a phenomenon known as slip.
As the rotor spins, it cuts through the stator’s magnetic field lines, inducing an electromagnetic force (EMF) in the rotor windings. This EMF opposes the applied voltage, limiting the current flow in the rotor. The interaction between the rotor currents and the stator’s magnetic field produces a torque that keeps the rotor spinning as long as the AC supply is maintained.

What Is Brushless DC Motor
A brushless DC (BLDC) motor is a type of synchronous electric motor that uses electronic commutation to control the current in the windings, eliminating the need for mechanical brushes. BLDC motors offer several advantages over traditional brushed DC motors, including higher efficiency, longer lifespan, and lower maintenance requirements.
The main components of a brushless DC motor include:
- Stator: The stationary part of the motor, consisting of a series of windings arranged in a specific pattern. The stator windings are energized by an external controller, creating a rotating magnetic field.
- Rotor: The rotating part of the motor, typically made of permanent magnets. The rotor is attracted to the rotating magnetic field generated by the stator, causing it to spin.
- Electronic Speed Controller (ESC): An electronic circuit that controls the power supply to the stator windings. The ESC receives input from a position sensor and determines the appropriate sequence and timing for energizing the windings to maintain smooth rotation.
- Position Sensor: A device that detects the position of the rotor and provides feedback to the ESC. Common types of position sensors include Hall effect sensors, optical encoders, and resolvers.
- Bearings: Support the rotor and allow it to rotate smoothly with minimal friction.
How Brushless DC Motors Work
Brushless DC (BLDC) motors operate on the principle of electromagnetic interaction between the rotor and stator. Unlike traditional brushed DC motors, BLDC motors do not use physical brushes for commutation. Instead, they rely on electronic commutation to control the current flow and maintain rotation.
The stator of a BLDC motor consists of windings arranged in a specific pattern, typically in a three-phase configuration. These windings are energized in a sequence by an electronic controller, which determines the timing and direction of current flow. The rotor, on the other hand, contains permanent magnets that interact with the magnetic field generated by the stator windings.
As the electronic controller energizes the stator windings in a specific sequence, it creates a rotating magnetic field. The permanent magnets on the rotor are attracted to this rotating field, causing the rotor to follow and spin in synchronization with the stator’s field. By precisely controlling the timing and duration of the current pulses sent to the stator windings, the electronic controller can regulate the speed and torque of the BLDC motor.

Key Differences Between Induction and DC Brushless Motors
Construction
Induction motors have a simple, rugged design consisting of a stator with windings and a rotor with conductors, typically in a squirrel cage configuration.
BLDC motors have a permanent magnet rotor and a stator with windings. The presence of permanent magnets in BLDC motors eliminates the need for a separate field winding, making their construction more compact.
Efficiency
BLDC motors generally offer higher efficiency compared to induction motors, especially at lower power ratings. The permanent magnets in BLDC motors create a strong magnetic field without the need for additional energy input, reducing losses associated with magnetizing current.
Induction motors rely on induced currents in the rotor, leading to higher rotor losses and lower efficiency.
Size and Weight
Due to their compact construction and the absence of a separate field winding, BLDC motors tend to have a smaller size and lower weight compared to induction motors of similar power ratings.
Maintenance Requirements
Induction motors are known for their low maintenance requirements due to their simple and robust construction. They have no brushes or commutators, reducing the need for regular maintenance.
BLDC motors also have low maintenance needs, as they lack brushes. However, the presence of permanent magnets in BLDC motors may require periodic inspection to ensure their integrity, especially in harsh operating conditions.
Torque Characteristics
BLDC motors exhibit excellent torque characteristics, providing high starting torque and precise speed control. The permanent magnets in BLDC motors enable fast acceleration and deceleration, making them suitable for applications requiring quick response times and accurate positioning.
Induction motors, while capable of producing high starting torque, may have limitations in terms of dynamic performance and speed control accuracy compared to BLDC motors.
Cost
In general, induction motors tend to be more cost-effective, especially for larger power ratings and simpler control requirements.
FAQs
Is a 3-phase induction motor brushless?
Yes, a 3-phase induction motor is brushless. Induction motors do not require brushes or a commutator for operation, as they rely on electromagnetic induction to generate torque. The stator windings create a rotating magnetic field, which induces currents in the rotor, causing it to rotate without any physical contact between the stator and rotor.
Is a DC motor and an induction motor the same?
No, a DC motor and an induction motor are not the same. DC motors operate on direct current and require a commutator and brushes to reverse the current direction in the armature windings. In contrast, induction motors operate on alternating current and do not require brushes or a commutator, relying instead on electromagnetic induction for operation.