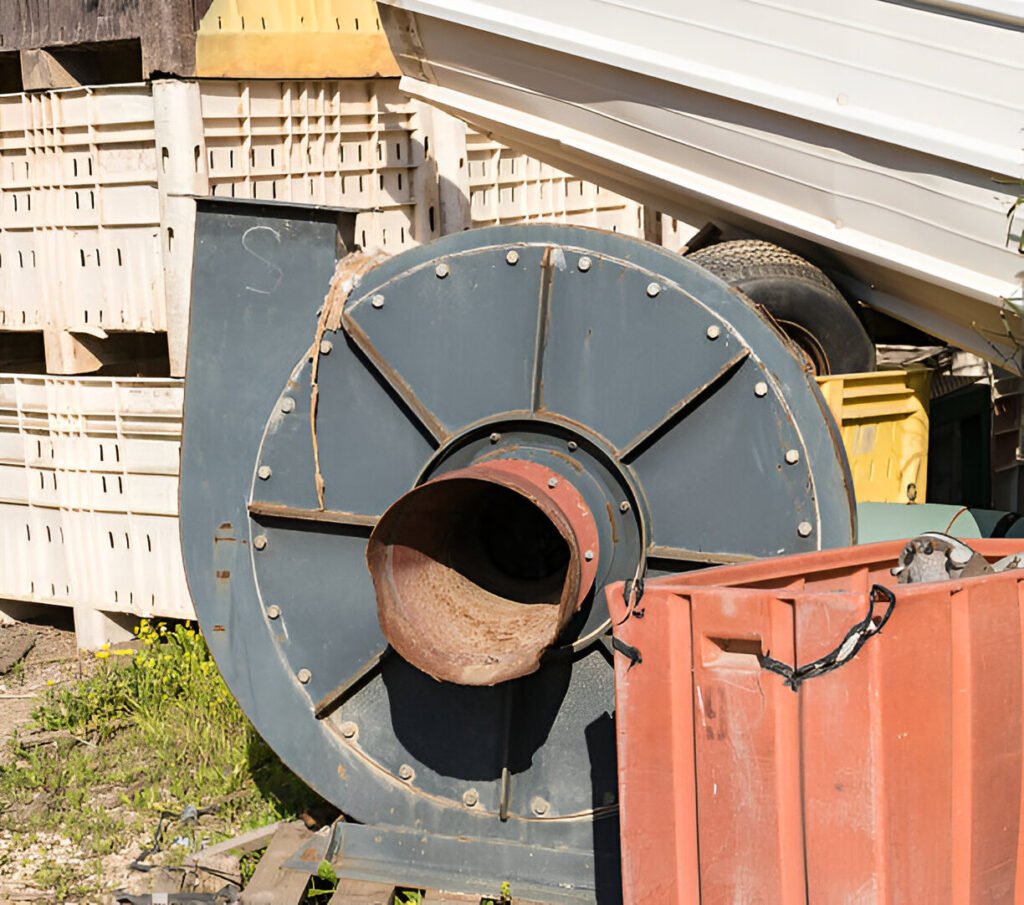
Types of Centrifugal Fans
Centrifugal fans are essential for many industrial applications, but with numerous types available, selecting the optimal fan can be challenging.
Making the wrong choice can lead to inefficiencies, increased energy costs, and subpar performance.
In this article, we’ll explore the five main types of centrifugal fans – forward-curved, backward-curved, radial, radial tip, and airfoil – and compare their efficiencies to help you make an informed decision for your specific application.
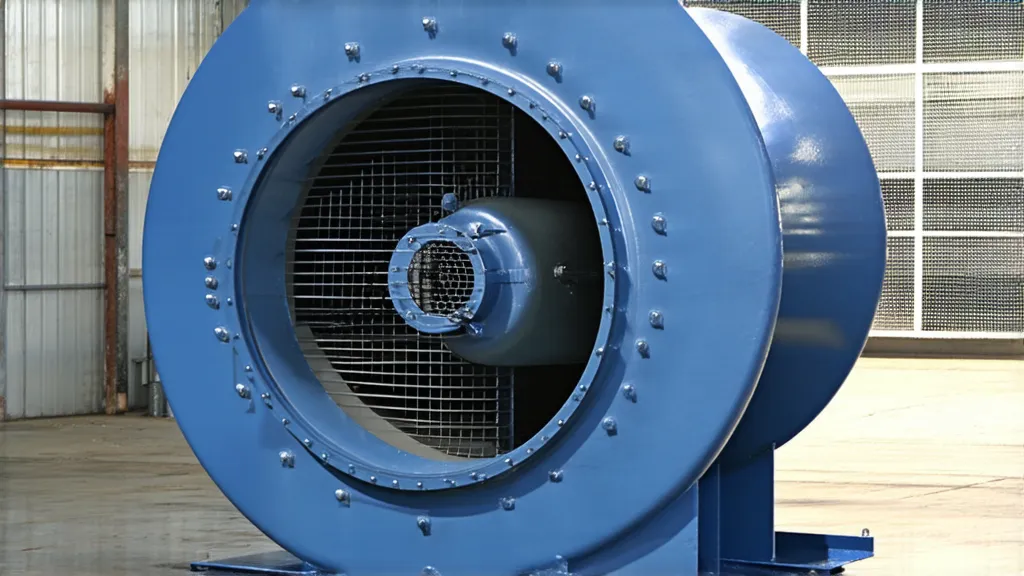
Forward-Curved Fans
Forward-curved fans, also known as squirrel cage fans, feature blades that curve in the direction of rotation. This blade configuration allows for high airflow volumes at lower pressures compared to other centrifugal fan types. The compact design and low noise levels of forward-curved fans make them suitable for applications such as HVAC systems, air conditioning units, and furnaces.
However, forward-curved fans have some limitations. They are less efficient than other centrifugal fan designs due to the curvature of the blades, which can lead to flow separation and increased turbulence. Additionally, their performance is more sensitive to changes in system resistance, making them less adaptable to varying operating conditions.
Backward-Curved Fans
In contrast to forward-curved fans, backward-curved fans have blades that curve against the direction of rotation. This blade design allows for higher efficiency and pressure capabilities compared to forward-curved fans. Backward-curved fans are well-suited for applications that require high pressure, such as industrial exhaust systems, material handling, and air pollution control.
There are two main types of backward-curved fans: backward-inclined and backward-airfoil. Backward-inclined fans have flat blades angled away from the direction of rotation, while backward-airfoil fans feature airfoil-shaped blades for even higher efficiency. Both types offer stable performance across a wide range of operating conditions and are less prone to overloading than forward-curved designs.
Radial Fans
Radial fans, also called straight-bladed fans, have blades that extend straight out from the hub, perpendicular to the direction of rotation. This simple blade geometry provides high pressure capabilities at lower airflow volumes compared to other centrifugal fan designs. Radial fans are commonly used in applications that require high pressures, such as industrial process ventilation, pneumatic conveying, and dust collection systems.
One advantage of radial fans is their durability and resistance to wear from dust and particulates. The straight blade design minimizes the accumulation of debris, making them suitable for handling dirty or abrasive airstreams. However, radial fans tend to be noisier than other centrifugal fan types due to the turbulence generated by the straight blades.
Radial Tip Fans
Radial tip fans are a variant of radial fans that feature a small forward curve at the tip of the blades. This blade design combines the high-pressure capabilities of radial fans with improved efficiency and reduced noise levels. The curved blade tips help to smoothly guide the airflow and reduce turbulence, resulting in quieter operation compared to straight-bladed radial fans.
Radial tip fans are often used in applications that require high pressures but also have noise restrictions, such as HVAC systems in commercial buildings, clean rooms, and laboratory exhaust systems.
Airfoil Fans
Airfoil fans have blades with a cross-section shaped like an aircraft wing, designed to optimize aerodynamic efficiency. This blade geometry allows for smooth, laminar airflow and minimal turbulence, resulting in the highest efficiency among centrifugal fan types. Airfoil fans can achieve efficiency levels up to 85-90%, significantly reducing energy consumption and operating costs.
In addition to their high efficiency, airfoil fans offer quiet operation and stable performance over a wide range of operating conditions. They are commonly used in applications that require large air volumes at moderate pressures, such as HVAC systems in large commercial buildings, power plants, and industrial ventilation systems.
However, airfoil fans are typically more expensive than other centrifugal fan designs due to their complex blade geometry and manufacturing process. They are also more sensitive to dust and debris accumulation, which can disrupt the laminar airflow and reduce efficiency over time.