Blowers are an essential component in a wide array of industrial applications, from pneumatic conveying to wastewater treatment. These powerful machines are designed to generate high volumes of air flow or gas pressure, making them indispensable in sectors such as manufacturing, energy production, and environmental management.
In this blog post, we will delve into the intricacies of blowers, exploring their operating principles, key components, and diverse applications across various industries.
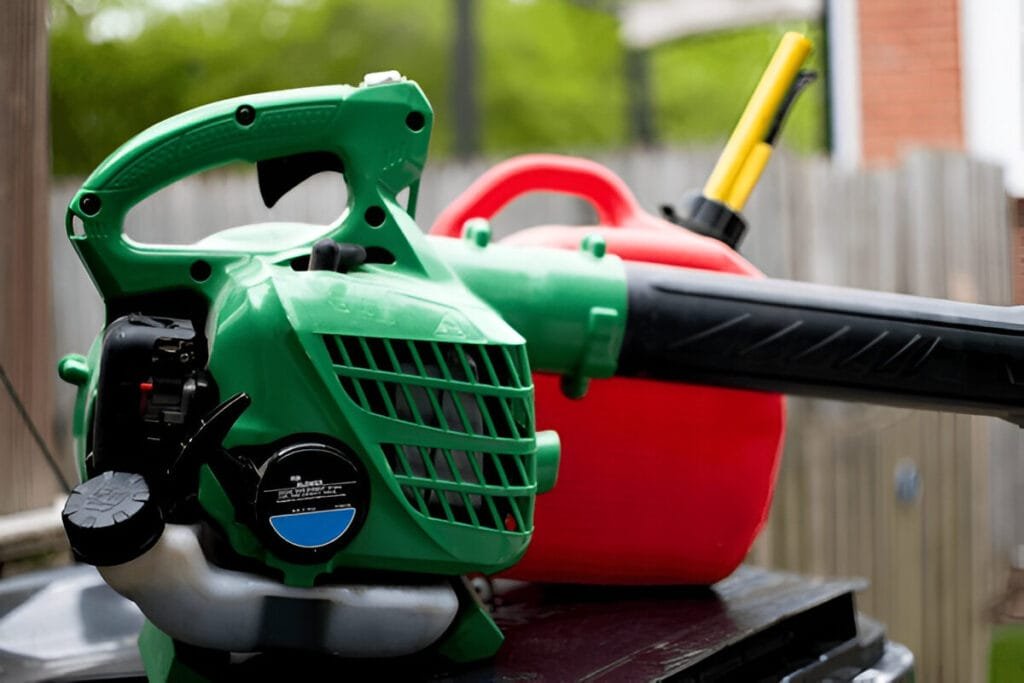
What Are Blowers
Blowers are mechanical devices designed to move air or other gases by generating a pressure differential. These versatile machines are used in a wide range of industrial, commercial, and residential applications to provide a steady flow of air or gas.
The primary function of a blower is to increase the velocity of air or gas, which in turn creates a pressure difference between the inlet and outlet. This pressure difference allows blowers to move large volumes of air or gas efficiently.
Discharge Pressure/Suction Pressure Ratio
Fans typically operate at low pressure ratios, usually not exceeding 1.1. This means that the discharge pressure is only slightly higher than the suction pressure.
Blowers operate at moderate pressure ratios, ranging from 1.1 to 1.2. They are capable of generating higher pressures than fans while still maintaining a significant airflow capacity.
Compressors are designed to operate at high pressure ratios, typically exceeding 1.2. They are capable of generating significantly higher discharge pressures compared to the suction pressure.
How Blowers Work
Blowers operate on the principle of converting mechanical energy into kinetic energy. Most blowers are powered by an electric motor or an internal combustion engine, which drives the blower’s impeller or rotor. As the impeller rotates, it draws air or gas into the blower housing and accelerates it outward through centrifugal force.
Types of Blowers
Centrifugal Blowers
Centrifugal blowers, also known as radial blowers, are one of the most common types of industrial blowers. They utilize centrifugal force generated by a rotating impeller to increase the velocity of air or gas, which is then converted into pressure.
Centrifugal blowers are known for their high flow rates and moderate pressure capabilities, making them suitable for a wide range of applications, such as pneumatic conveying, dust control, and ventilation systems.
Multistage Blowers
Multistage blowers, also referred to as multi-stage centrifugal blowers, consist of multiple impellers arranged in series. Each stage further increases the pressure of the air or gas, allowing these blowers to achieve higher discharge pressures compared to single-stage centrifugal blowers.
Multistage blowers are commonly used in applications that require high-pressure air, such as water treatment, chemical manufacturing, and gas boosting.
Axial Blower
Axial blowers, also known as axial fans, move air or gas along the axis of the blower. They feature a propeller-like rotor with blades that force the air to move parallel to the shaft.
Axial blowers are typically used in applications that require high flow rates and low-pressure ratios, such as cooling systems, ventilation, and exhaust systems.
Positive Displacement Blowers
Positive displacement blowers, also called PD blowers, work by trapping a fixed volume of air or gas and moving it through the blower.
There are two main types of positive displacement blowers: rotary lobe blowers and helical screw blowers.
- Rotary Lobe Blowers
Rotary lobe blowers feature two intermeshing lobes that rotate in opposite directions, trapping and moving air or gas through the blower.
They provide a constant flow rate and are suitable for applications that require low to moderate pressures, such as wastewater treatment, pneumatic conveying, and aeration.
- Helical Screw Blowers
Helical screw blowers, also known as positive displacement screw blowers, consist of two intermeshing helical screws that compress and move air or gas. They are known for their energy efficiency, quiet operation, and ability to handle a wide range of gases.
Helical screw blowers are commonly used in applications such as pneumatic conveying, wastewater treatment, and food processing.
Regenerative Blowers
Regenerative blowers, also called side channel blowers or ring compressors, use an impeller with backward-curved blades to generate airflow. As the impeller rotates, air is drawn into the blower and accelerated through a ring-shaped channel, creating a high-velocity airstream.
Regenerative blowers are compact and can achieve high pressures with relatively low flow rates, making them suitable for applications such as vacuum lifting, air knives, and dental equipment.
Turbo Blowers
Turbo blowers, also known as turbo compressors, use a high-speed turbine to compress air or gas. They are similar to centrifugal blowers but operate at much higher speeds and can achieve higher pressure ratios.
Turbo blowers are highly efficient and are commonly used in wastewater treatment plants, pneumatic conveying systems, and other industrial applications that require a reliable and efficient source of compressed air.
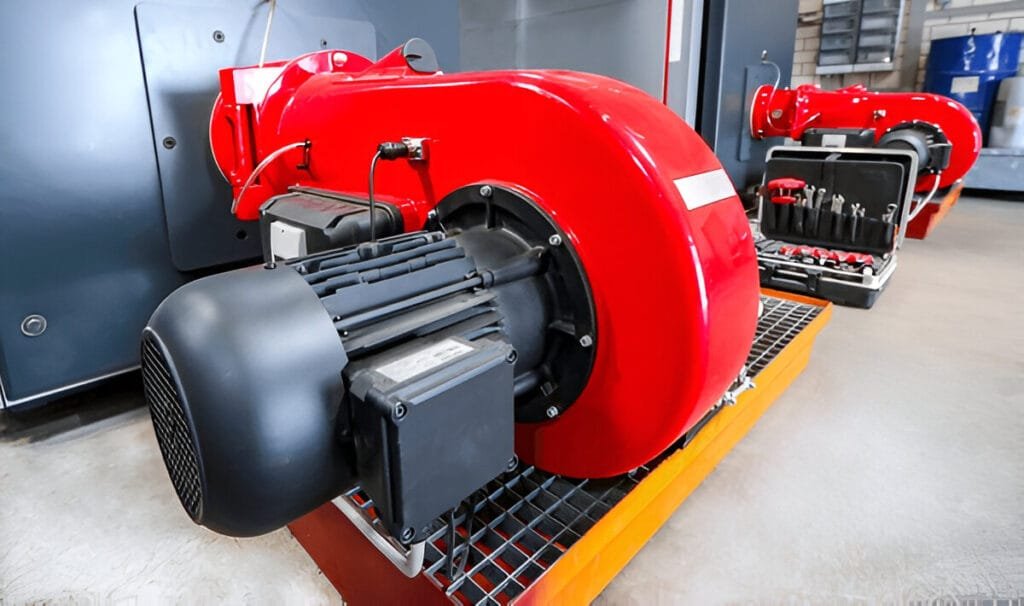
Advantages of Using Blowers
Energy Efficiency
Blowers are designed to move large volumes of air or gas while consuming minimal energy. The energy efficiency of blowers translates to lower operating costs and reduced environmental impact.
Versatility
Blowers offer a wide range of applications across various industries. They can be used for ventilation, cooling, drying, air pollution control, and pneumatic conveying.
Durability and Reliability
Blowers are constructed using durable materials such as stainless steel or carbon steel, ensuring long-lasting performance in demanding environments.
Customization Options
Blower manufacturers offer a wide range of customization options to meet specific application requirements. Blowers can be tailored in terms of size, capacity, pressure, and flow rate to suit particular industrial processes.
Applications of Blowers
Industrial Applications
In the manufacturing sector, blowers are employed for ventilation, cooling, and drying purposes. They help maintain a safe and comfortable working environment by removing heat, fumes, and airborne contaminants.
Blowers are also used in pneumatic conveying systems to transport bulk materials such as powders, granules, and pellets efficiently.
In the water treatment industry, blowers provide aeration and mixing of liquids, promoting biological processes and improving water quality.
Commercial Applications
In the food and beverage industry, blowers are used for drying, cooling, and packaging processes. They help preserve product quality and extend shelf life by removing moisture and regulating temperature.
In the healthcare sector, blowers are utilized in medical equipment, such as ventilators and artificial lungs, to provide precise and consistent airflow.
Residential Applications
In home ventilation systems, blowers circulate fresh air and remove stale or polluted air, improving indoor air quality.
Blowers are also found in household appliances such as vacuum cleaners and air conditioners, where they create suction or facilitate air circulation for effective cleaning and temperature control.