AC motors are the powerhouses behind countless industrial applications, converting electrical energy into mechanical motion with remarkable efficiency. These versatile machines have revolutionized the machinery industry, enabling the automation and optimization of processes across various sectors.
In this blog post, we will delve into the intricacies of AC motors, exploring their fundamental principles, types, and applications.

What is an AC Motor
An AC motor, short for alternating current motor, is an electric motor driven by an alternating current (AC) power source. AC motors are widely used in various applications due to their simple design, reliable operation, and ability to convert electrical energy into mechanical energy efficiently.
There are two primary types of AC motors: induction motors and synchronous motors. Induction motors, also known as asynchronous motors, rely on the induced current in the rotor to create a magnetic field that interacts with the stator’s field, resulting in rotational motion. Synchronous motors, on the other hand, have a rotor that rotates at the same speed as the stator’s magnetic field, making them ideal for applications requiring precise speed control.
AC motors offer several advantages over their DC counterparts, including simple construction, lower maintenance requirements, and the ability to operate directly from an AC power source without the need for complex control circuitry. They are also available in a wide range of sizes, power outputs, and configurations to suit various industrial and commercial applications.
How AC Motors Work
The working principle of AC motors is based on the interaction between magnetic fields generated by the stator and rotor. The stator is the stationary part of the motor, typically consisting of a set of windings arranged in a specific pattern. When an alternating current flows through the stator windings, it creates a rotating magnetic field.
The rotor, which is the rotating part of the motor, is positioned inside the stator. It can be either a wound rotor, where the rotor windings are connected to an external power source through slip rings and brushes, or a squirrel cage rotor, which consists of conductor bars embedded in the rotor core and short-circuited by end rings.
As the stator’s magnetic field rotates, it induces currents in the rotor conductors. These induced currents generate their own magnetic field, which interacts with the stator’s field. The interaction between the stator and rotor magnetic fields produces a torque, causing the rotor to rotate and generate mechanical power.
The speed of the rotor in an AC motor depends on the frequency of the supplied alternating current and the number of magnetic poles in the stator. In most cases, the rotor rotates at a slightly lower speed than the synchronous speed, which is determined by the frequency and number of poles. This difference in speed is called slip, and it allows for efficient power transfer from the stator to the rotor.
Components of AC Motors
- Stator: The stationary part of the motor, consisting of a series of wire coils wound around a magnetic core. The stator produces a rotating magnetic field when supplied with alternating current.
- Rotor: The rotating part of the motor, typically made of conductive bars or windings arranged in a cylindrical shape. The rotor interacts with the stator’s magnetic field, causing it to rotate.
- Bearings: Support the rotor and allow it to rotate smoothly within the stator. Bearings reduce friction and ensure proper alignment of the rotor.
- Frame: The outer casing of the motor, providing mechanical support and protection for the internal components. The frame also acts as a heat sink, dissipating heat generated by the motor.
- Windings: Insulated copper wire coils wound around the stator and rotor cores. The stator windings create the rotating magnetic field, while the rotor windings (if present) carry induced currents.
- Shaft: The rotating output shaft of the motor, which transmits mechanical power to the connected load. The shaft is coupled to the rotor and supported by bearings.
- Fan: A cooling fan attached to the shaft or rotor, designed to circulate air and dissipate heat generated by the motor during operation.
- Terminal box: An enclosure on the motor housing that contains the electrical connections for power supply and control wiring.
Types of AC Motors
There are two main types of AC motors: induction motors and synchronous motors.
Induction Motors
Induction motors, also known as asynchronous motors, are the most common type of AC motor. They rely on electromagnetic induction for operation, hence their name. Key components of an induction motor include the stator, which is stationary, and the rotor, which rotates inside the stator.
The stator consists of windings that, when energized with AC current, create a rotating magnetic field. This rotating field induces currents in the rotor conductors, generating a magnetic field that interacts with the stator’s field. The interaction between these two fields produces torque, causing the rotor to turn.
Synchronous Motors
Synchronous motors operate at a constant speed determined by the frequency of the supplied AC power and the number of motor poles. The rotor in a synchronous motor rotates at the same speed as the stator’s magnetic field, hence the name “synchronous.”
The rotor of a synchronous motor can be of two types: salient pole or cylindrical. Salient pole rotors have projecting magnetic poles with concentrated windings, while cylindrical rotors have a smooth surface with distributed windings.
In synchronous motors, the rotor’s magnetic field is typically generated by either permanent magnets or DC excitation through slip rings. The interaction between the rotor’s magnetic field and the stator’s rotating magnetic field produces torque, causing the rotor to synchronize with the stator’s field.
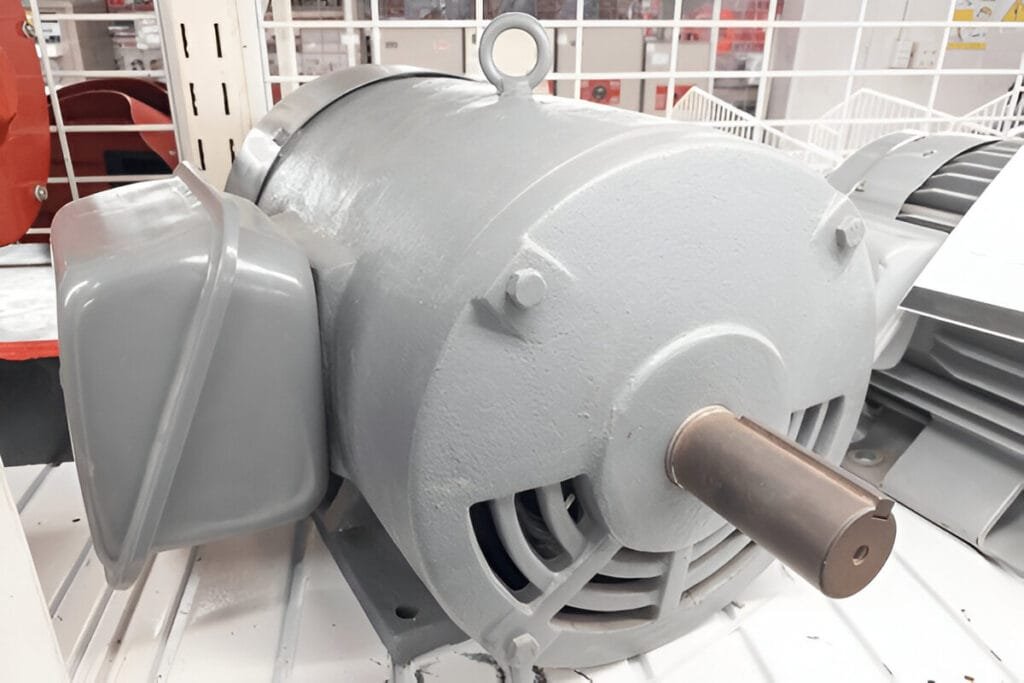
Advantages of AC Motors
High Efficiency
AC motors, particularly induction motors, are known for their excellent energy efficiency compared to other types of electric motors. The simple design and lack of brushes or commutators in AC motors contribute to reduced energy losses and improved overall efficiency.
Low Maintenance
The absence of brushes and commutators in most AC motor types eliminates the need for regular brush replacement and maintenance.
Wide Range of Speeds
By adjusting the frequency of the AC power supply, the speed of an AC motor can be easily controlled.
Durability and Reliability
The robust construction and absence of delicate components like brushes contribute to their long lifespan and resistance to wear and tear. AC motors are designed to withstand harsh operating conditions, such as high temperatures, dust, and moisture, making them suitable for industrial environments.
Applications of AC Motors
Industrial Machinery
AC motors are commonly employed in conveyor systems, pumps, compressors, fans, and machine tools.
In manufacturing plants, AC motors power assembly lines, packaging machines, and material handling equipment, ensuring smooth and efficient production processes.
HVAC Systems
AC motors are used in air handlers, cooling towers, and refrigeration units to circulate air and transfer heat.
In residential and commercial buildings, AC motors ensure comfortable indoor environments by powering fans, blowers, and compressors in HVAC systems.
Home Appliances
AC motors are widely used in household appliances such as washing machines, dryers, refrigerators, and vacuum cleaners.
In washing machines, AC motors drive the agitator and spin cycle, while in refrigerators, they power the compressor for cooling.
Transportation
The high efficiency and torque characteristics of AC motors make them well-suited for propelling EVs and HEVs. In these vehicles, AC motors convert electrical energy from the battery into mechanical energy to drive the wheels.
The precise speed control and regenerative braking capabilities of AC motors contribute to the overall efficiency and performance of electric and hybrid vehicles.