Efficient ventilation and air movement are paramount in various industrial environments to maintain optimal working conditions and ensure the safety of personnel. Centrifugal exhaust fans have emerged as a reliable solution for managing airflow in these settings.
This blog post delves into the intricacies of centrifugal exhaust fans, exploring their working principles, the different types available, and their distinct advantages and disadvantages.
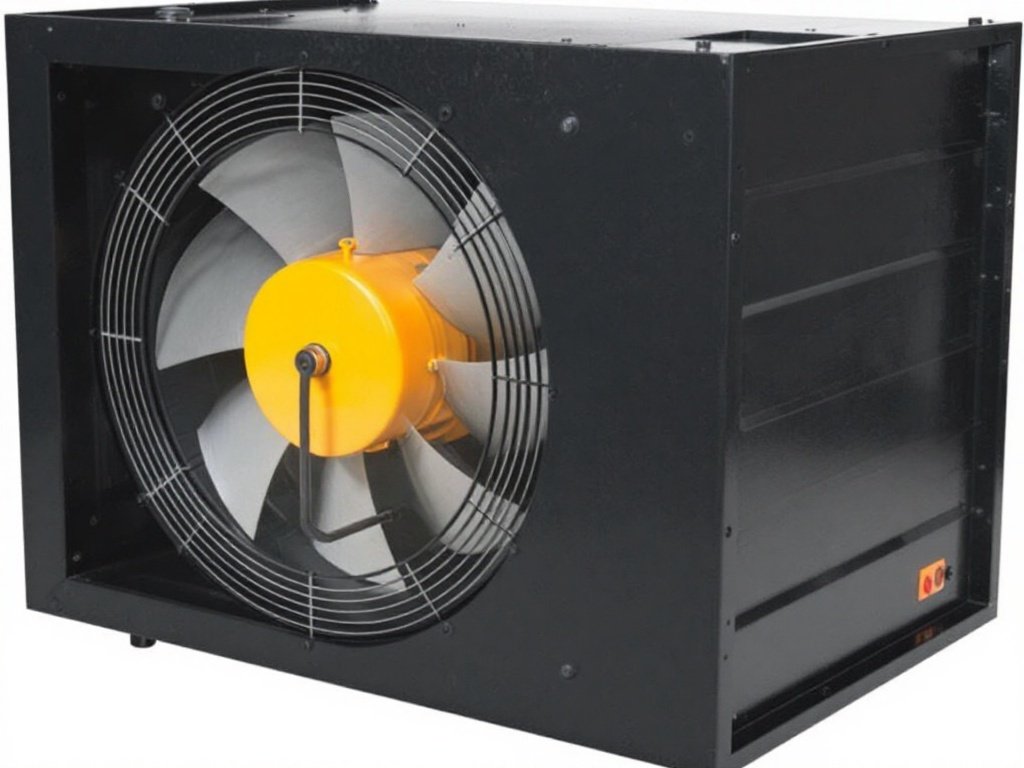
What Is a Centrifugal Exhaust Fan
A centrifugal exhaust fan is a mechanical device designed to move air or other gases from one location to another. It is commonly used in industrial, commercial, and residential settings for ventilation, cooling, and exhaust purposes.
Centrifugal exhaust fans consist of a rotating impeller housed within a stationary casing. The impeller is composed of a series of blades that are mounted on a central hub. As the impeller rotates, it draws air into the center of the fan and accelerates it radially outward through the blades.
The centrifugal force generated by the rotating impeller increases the pressure of the air, allowing it to overcome resistance and move through the exhaust system. The casing surrounding the impeller helps to guide the airflow and improve the efficiency of the fan.
How Does a Centrifugal Exhaust Fan Work
The working principle of a centrifugal exhaust fan is based on the concept of centrifugal force. When the impeller rotates, it creates a pressure difference between the inlet and outlet of the fan. This pressure difference causes air to flow from the high-pressure region to the low-pressure region.
The process can be broken down into several steps:
- Air enters the fan through the inlet, which is typically located at the center of the impeller.
- As the impeller rotates, the blades capture the air and accelerate it radially outward.
- The centrifugal force generated by the rotating impeller increases the pressure of the air as it moves through the blades.
- The high-pressure air is then directed through the outlet of the fan, which is typically connected to ductwork or piping.
- The continuous rotation of the impeller maintains the airflow, allowing the fan to effectively move air from one location to another.
Types of Centrifugal Exhaust Fans
Forward-Curved Blade Fans
Forward-curved blade fans feature blades that curve towards the direction of rotation. This design allows for high airflow rates at low pressures, making them suitable for applications requiring high volumes of air movement, such as air conditioning systems and ventilation in large spaces.
The compact size of forward-curved blade fans enables their installation in limited spaces. However, they are less energy-efficient compared to other centrifugal fan types and are more prone to accumulating dust and debris on the blades, which can lead to reduced performance over time.
Backward-Curved Blade Fans
Backward-curved blade fans have blades that curve away from the direction of rotation. This design provides high energy efficiency and is capable of operating at higher pressures compared to forward-curved blade fans.
There are two main types of backward-curved blade fans: single-thickness blades and airfoil blades. Single-thickness blades are more economical and suitable for general-purpose applications, while airfoil blades offer higher efficiency and lower noise levels, making them ideal for HVAC systems and industrial processes requiring precise airflow control.
Backward-curved blade fans are less prone to dust and debris accumulation, resulting in more consistent performance over time. However, they may require larger installation spaces compared to forward-curved blade fans.
Radial Blade Fans
Radial blade fans, also known as straight blade fans, have blades that extend straight outward from the hub. This design allows for the handling of high pressures and temperatures, making them suitable for industrial applications such as exhaust systems, material conveying, and dust collection.
Radial blade fans are further classified into three sub-types based on blade thickness: SWSI (Single Width Single Inlet), DWDI (Double Width Double Inlet), and industrial exhausters. SWSI fans are compact and suitable for space-constrained installations, while DWDI fans offer higher airflow rates and pressure capabilities. Industrial exhausters are designed for heavy-duty applications involving corrosive or abrasive materials.
Radial blade fans are known for their durability and ability to handle demanding operating conditions. However, they are less energy-efficient compared to backward-curved blade fans and may generate higher noise levels.
Advantages of Centrifugal Exhaust Fans
High Efficiency
Centrifugal exhaust fans offer high efficiency in moving air, particularly in systems with high static pressure. The fan wheel’s design allows for efficient conversion of rotational kinetic energy into increased pressure, enabling the fan to overcome resistance in the ductwork.
Durability
These fans are built to withstand demanding industrial environments. The robust construction, often featuring heavy-gauge steel housings and wheels, ensures long-lasting performance even under continuous operation.
Versatility
Centrifugal exhaust fans come in a wide range of sizes and configurations, making them adaptable to various applications. They can be customized with different wheel types, drive arrangements, and motor options to suit specific performance requirements.
Ability to Handle Harsh Environments
Centrifugal fans are well-suited for handling high temperatures, dust-laden air, and corrosive gases. Special materials and coatings can be used to enhance their resistance to harsh conditions, ensuring reliable operation in challenging environments.
Disadvantages of Centrifugal Exhaust Fans
Noise Generation
Centrifugal fans can generate significant noise levels, especially at high speeds or when handling large volumes of air. The noise is primarily due to turbulence and the interaction of the air with the fan blades. Proper installation and the use of sound attenuation measures may be necessary to mitigate noise issues.
Size and Weight
Compared to axial fans, centrifugal exhaust fans are generally larger and heavier for a given airflow capacity. This can pose challenges in terms of space requirements and structural support, particularly in retrofit applications or when space is limited.
Higher Initial Cost
The construction and materials used in centrifugal fans often result in a higher initial cost compared to other types of fans. However, their durability and efficiency can offset this over the fan’s life cycle, making them a cost-effective choice in the long run.
Applications of Centrifugal Exhaust Fans
Industrial Ventilation
Centrifugal fans are widely used in industrial settings for general ventilation, process exhaust, and pollution control. They are effective in removing heat, fumes, dust, and other airborne contaminants from manufacturing plants, warehouses, and production facilities.
Commercial Kitchen Exhaust
In commercial kitchens, centrifugal exhaust fans play a vital role in removing heat, steam, and grease-laden vapors from cooking operations. They are designed to handle the high temperatures and grease accumulation associated with kitchen exhaust systems.
Laboratories and Clean Rooms
Centrifugal fans are employed in laboratories and clean rooms to maintain precise airflow control and pressure relationships. They assist in removing potentially hazardous fumes, particulates, and maintaining the required air change rates for these sensitive environments.
HVAC Systems
In heating, ventilation, and air conditioning (HVAC) systems, centrifugal fans are used for air distribution and exhaust purposes. They are commonly found in air handling units, rooftop units, and ductwork systems, ensuring proper circulation and removal of conditioned air.