Brushed DC electric motors are simple yet powerful electric motors found in various applications. They convert electrical energy into mechanical energy through a straightforward process involving magnetic fields and current flow.
In this article, we will explore the working principle, key components, types, advantages, and disadvantages of brushed DC motors.
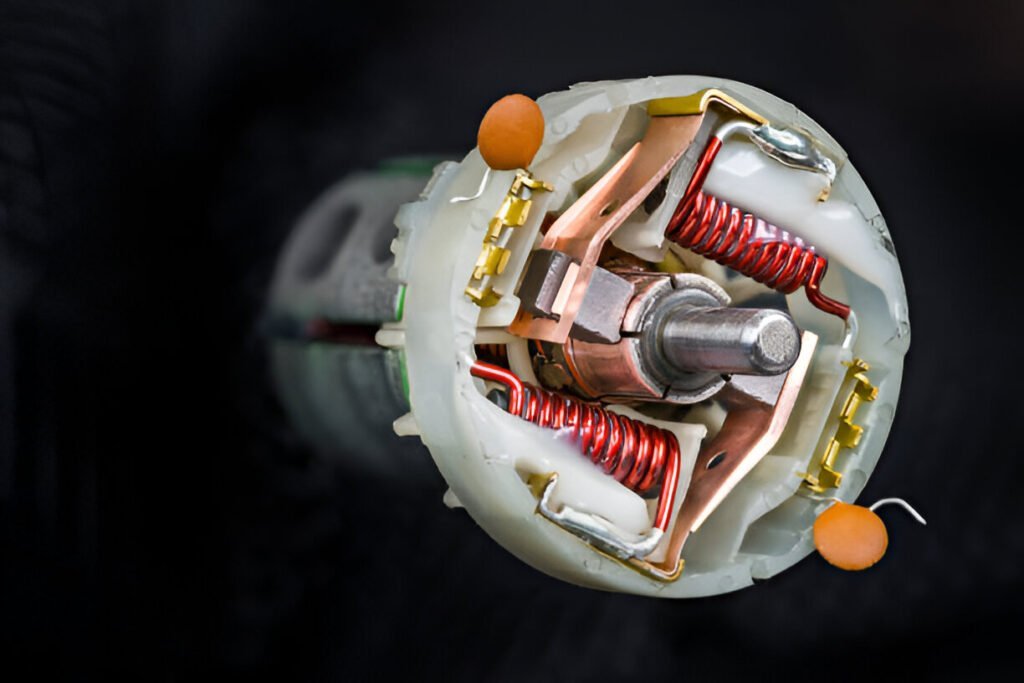
What Are Brushed Dc Motors
Brushed DC motors are a type of electric motor that converts direct current (DC) electrical energy into mechanical energy. These motors rely on a commutator and brushes to control the direction of current flow in the armature windings, which enables continuous rotation.
When a DC voltage is applied to the motor, current flows through the brushes and commutator, energizing the armature windings. The magnetic fields created by the armature interact with the stator’s magnetic field, causing the rotor to rotate. As the rotor turns, the commutator continuously switches the direction of current flow in the armature windings, maintaining the torque and rotation of the motor.
Working Principle of Brushed Dc Motors
A brushed DC motor converts electrical energy into mechanical energy through a process called electromechanical conversion.
Current Flow and Magnetic Fields
When current flows through the armature windings, it generates a magnetic field around the rotor. This magnetic field interacts with the permanent magnets on the stator, creating a force that causes the rotor to spin.
As the rotor spins, the commutator reverses the current flow in the armature windings at specific points, ensuring that the rotor continues to rotate in the same direction. This process is known as commutation.
Higher current flow through the armature windings results in a stronger magnetic field, which in turn produces greater torque.
Role of Back EMF
As the rotor spins within the magnetic field, it generates a voltage in the opposite direction of the applied voltage, known as back EMF. This voltage opposes the current flow through the motor windings, effectively regulating the motor’s speed and preventing excessive current draw.
The magnitude of the back EMF is directly proportional to the motor’s speed. As the motor spins faster, the back EMF increases, reducing the net voltage across the motor windings and limiting the current flow. This inherent feedback mechanism helps maintain a stable operating speed under varying load conditions.
Back EMF also contributes to the motor’s efficiency by minimizing power losses. Without back EMF, the motor would draw excessive current, leading to increased heat generation and reduced efficiency. By opposing the applied voltage, back EMF helps optimize the motor’s performance and prevents damage to the windings and other components.
Types of Brushed DC Motors
Permanent Magnet Motors
Permanent magnet (PM) motors feature a stator with permanent magnets and a wound rotor (armature). The permanent magnets create a constant magnetic field, eliminating the need for an external field winding. PM motors offer high efficiency, compact size, and excellent speed control, making them suitable for applications such as automotive accessories, power tools, and small appliances.
Shunt-Wound Motors
Shunt-wound motors have both the armature and field windings connected in parallel (shunt) to the power supply. The field winding is composed of many turns of thin wire, creating a strong, constant magnetic field. Shunt-wound motors provide good speed regulation and are suitable for applications requiring constant speed under varying loads, such as conveyors, pumps, and machine tools.
Series-Wound Motors
In series-wound motors, the armature and field windings are connected in series, sharing the same current. The field winding consists of a few turns of thick wire, creating a magnetic field proportional to the armature current. Series-wound motors offer high starting torque and are ideal for applications requiring high initial loads, such as cranes, hoists, and electric vehicles. However, they have poor speed regulation and may overspeed if the load is removed.
Key Components of Brushed DC Motors
- Stator: The stator is the stationary part of the brushed DC motor. It consists of a cylindrical frame that houses the permanent magnets or field windings, depending on the motor type. The stator provides a constant magnetic field that interacts with the rotor’s magnetic field to generate torque and facilitate motor rotation.
- Rotor (Armature): The rotor, also known as the armature, is the rotating part of the brushed DC motor. It is made up of a laminated iron core with multiple windings wrapped around it. The rotor windings are connected to the commutator, which allows current to flow through them. As current passes through the rotor windings, a magnetic field is generated, which interacts with the stator’s magnetic field to produce torque.
- Commutator: The commutator is a cylindrical component mounted on the rotor shaft. It consists of a series of copper segments arranged in a circular pattern, with each segment connected to the ends of the rotor windings. The commutator acts as a mechanical switch, reversing the current direction in the rotor windings as the rotor rotates, ensuring continuous rotation in the same direction.
- Brushes: Brushes are small, spring-loaded components that press against the commutator. They are typically made of carbon or graphite and are responsible for conducting electrical current from the power source to the rotor windings via the commutator. As the commutator rotates, the brushes maintain contact with the commutator segments, allowing current to flow through the appropriate rotor windings based on the rotor’s position.

Advantages of Brushed DC Motors
- High Starting Torque: Brushed DC motors offer excellent starting torque, allowing them to quickly accelerate and overcome initial resistance.
- Ease of Control: Controlling the speed and torque of brushed DC motors is relatively simple. By varying the voltage applied to the motor, you can easily adjust its speed and torque output.
- Cost-Effectiveness: Brushed DC motors are generally more affordable compared to their brushless counterparts. The simpler design and manufacturing process of brushed motors contribute to their lower cost.
- Simplicity of Design: The design of brushed DC motors is relatively simple and straightforward. This simplicity in design makes brushed motors easier to manufacture, maintain, and repair compared to more complex motor types.
- Ease of Use in Various Applications: Brushed DC motors are versatile and can be used in a wide range of applications.
Disadvantages of Brushed DC Motors
- Maintenance Challenges: Brushed DC motors require regular maintenance due to the wear and tear of the brushes and commutator. As the brushes constantly make and break contact with the commutator, they gradually wear down, leading to reduced performance and the need for replacement.
- Efficiency Concerns: Brushed DC motors have inherent inefficiencies due to the friction between the brushes and the commutator. This friction leads to energy losses in the form of heat, reducing the overall efficiency of the motor. Additionally, the voltage drop across the brushes contributes to further energy losses. As a result, brushed DC motors typically have lower efficiency compared to brushless DC motors or other advanced motor technologies.
- Electrical Noise: The commutation process in brushed DC motors generates electrical noise, known as brush noise or commutator noise. As the brushes make and break contact with the commutator segments, sparking occurs, causing electromagnetic interference (EMI) and radio frequency interference (RFI).
- Longevity: The lifespan of brushed DC motors is limited by the wear and tear of the brushes and commutator. As the brushes continuously rub against the commutator, they gradually erode, leading to increased friction, reduced performance, and eventual failure. The constant sparking and heat generated during commutation also contribute to the degradation of the brushes and commutator. Consequently, brushed DC motors typically have a shorter lifespan compared to brushless DC motors, which do not have these wearing components.
- Performance: While brushed DC motors offer high starting torque, their performance can be limited in certain aspects. The presence of brushes and the commutator introduces mechanical limitations, such as maximum speed and power density. As the motor speed increases, the brushes may struggle to maintain proper contact with the commutator, leading to reduced performance and increased wear. Additionally, the friction and inertia of the brushes can limit the motor’s ability to achieve high speeds or rapid acceleration.
Applications of Brushed Dc Motors
- Automotive Industry: Brushed DC motors are widely used in automotive applications, such as windshield wipers, power windows, and seat adjustments.
- Power Tools: Brushed DC motors are commonly found in power tools like drills, saws, and sanders.
- Robotics: Brushed DC motors are used in various robotics applications, including hobby projects and industrial robots.
- Household Appliances: Many household appliances, such as blenders, mixers, and vacuum cleaners, utilize brushed DC motors.
- Toys and Hobbies: Brushed DC motors are popular in toys and hobby applications, such as remote-controlled cars, model trains, and small robots.
- Medical Equipment: Some medical devices, such as pumps and small actuators, rely on brushed DC motors.
- Industrial Automation: Brushed DC motors are used in various industrial automation applications, such as conveyor systems, packaging machines, and material handling equipment.
- Aerospace and Defense: Brushed DC motors find applications in aerospace and defense systems, such as control surfaces, actuators, and positioning systems.