Fans are integral components in various industrial machinery and equipment, facilitating air movement, cooling, and ventilation. Two common fan types used in industrial settings are centrifugal fans and EC (electronically commutated) fans, each with unique characteristics and advantages.
In this blog post, we will delve into the key differences between centrifugal fans and EC fans, exploring aspects such as design, operation principles, efficiency, control, noise levels, energy consumption, maintenance requirements, cost, and typical applications. By understanding these distinctions, professionals can make informed decisions when selecting the most suitable fan type for their specific industrial needs.
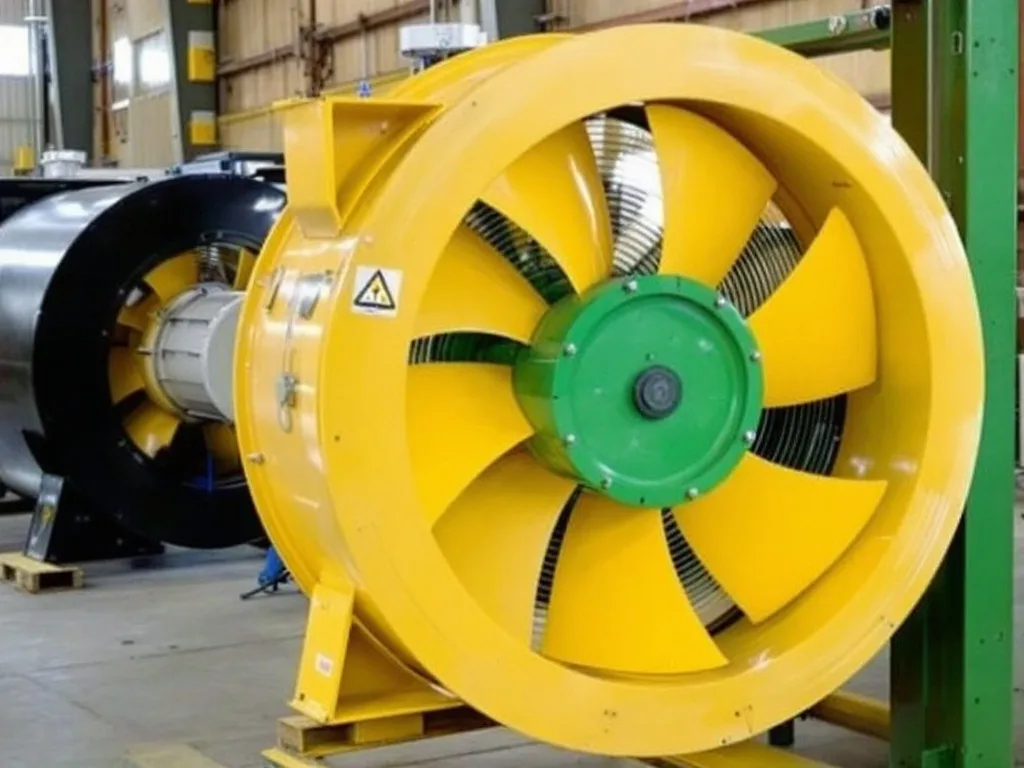
What Is Centrifugal Fan
A centrifugal fan is a mechanical device that utilizes rotating impellers to move air or gases. It consists of a fan wheel composed of a number of fan blades, ranging from 4 to 64, mounted around a hub. As the impeller rotates, it draws air into the center of the fan wheel and accelerates it radially outward by centrifugal force.
The centrifugal fan housing is typically scroll-shaped, collecting the air from the impeller and guiding it to the fan outlet. The impeller blades can be forward-curved, backward-inclined, backward-curved, or airfoil-shaped, depending on the application requirements.
Centrifugal fans are known for their ability to generate high pressure and handle large volumes of air. They are widely used in industrial, commercial, and residential applications such as ventilation systems, air conditioning units, exhaust systems, and process cooling.
What Is EC Fan
An EC (Electronically Commutated) fan, also known as a brushless DC fan, is a high-efficiency electric motor-driven fan that combines the benefits of AC and DC motors. EC fans use permanent magnet motors with built-in electronic commutation systems to control the motor’s speed and torque.
EC fans offer several advantages over traditional AC fans. They have higher efficiency, as the motor can operate at optimal speed for the required airflow and pressure. The electronic control system allows for precise speed regulation, enabling better temperature and airflow management. EC fans also generate less noise and have a longer lifespan due to the absence of mechanical brushes.
The compact design and integrated control electronics of EC fans make them suitable for a wide range of applications, including HVAC systems, refrigeration units, data centers, and telecommunications equipment. They are increasingly popular due to their energy-saving capabilities and the ability to adapt to various system requirements.
Key Differences Between Centrifugal Fans and EC Fans
Design
Centrifugal fans and EC fans differ significantly in their design. Centrifugal fans consist of a rotating impeller housed within a scroll-shaped casing. The impeller is typically composed of a series of blades or vanes that draw air in from the center and propel it radially outward.
In contrast, EC fans feature a compact, integrated design that combines the motor, control electronics, and impeller into a single unit. The impeller in an EC fan is directly attached to the motor, eliminating the need for belts or other mechanical transmission components.
Operation Principle
The operation principle of centrifugal fans and EC fans is fundamentally different. Centrifugal fans rely on the centrifugal force generated by the rotating impeller to increase the velocity and pressure of the air. As the impeller spins, it draws air in from the center and forces it outward through the blades, creating a high-velocity airflow.
EC fans, on the other hand, utilize electronically commutated motors (ECMs) to drive the impeller. ECMs are brushless DC motors that incorporate integrated electronic control circuitry. This allows for precise speed control and efficient operation across a wide range of operating conditions.
Efficiency
EC fans generally offer higher efficiency compared to centrifugal fans. The integrated design of EC fans minimizes energy losses associated with mechanical transmission components. Additionally, the electronically commutated motors used in EC fans provide more efficient power conversion and can maintain high efficiency levels even at reduced speeds.
Centrifugal fans, while still capable of efficient operation, may experience efficiency losses due to factors such as belt drive losses, impeller design limitations, and reduced efficiency at lower speeds.
Control
The control capabilities of EC fans surpass those of centrifugal fans. EC fans feature built-in electronic control circuitry that allows for precise speed regulation, enabling them to adapt to varying system requirements. This control flexibility allows EC fans to optimize airflow and energy consumption based on the specific needs of the application.
Centrifugal fans typically rely on external speed control methods, such as variable frequency drives (VFDs) or dampers, to adjust airflow. While these methods can provide some level of control, they may not offer the same level of precision and efficiency as the integrated control in EC fans.
Noise
EC fans generally produce lower noise levels compared to centrifugal fans. The compact, integrated design of EC fans reduces vibration and turbulence, resulting in quieter operation. Additionally, the ability to precisely control the speed of EC fans allows for optimized noise performance across different operating conditions.
Centrifugal fans, particularly at high speeds, can generate significant noise due to factors such as impeller design, airflow turbulence, and mechanical vibrations. Noise reduction measures, such as sound attenuators or vibration isolation, may be necessary to mitigate noise issues in centrifugal fan applications.
Energy Consumption
EC fans are known for their energy efficiency, consuming less power compared to centrifugal fans for equivalent airflow performance. The electronically commutated motors in EC fans enable efficient power conversion and can maintain high efficiency levels even at reduced speeds. This efficiency translates to lower energy consumption and operating costs.
Centrifugal fans, while still capable of efficient operation, may consume more energy due to factors such as belt drive losses, impeller design limitations, and reduced efficiency at lower speeds. The energy consumption of centrifugal fans can be optimized through proper sizing, selection of efficient components, and the use of variable speed controls.
Maintenance
EC fans generally require less maintenance compared to centrifugal fans. The integrated design of EC fans eliminates the need for regular maintenance tasks associated with belt drives, such as belt tensioning and replacement. Additionally, the brushless motor technology used in EC fans reduces wear and tear, extending the overall lifespan of the fan.
Centrifugal fans, particularly those with belt drives, require regular maintenance to ensure optimal performance and reliability. This may include tasks such as belt inspections, tensioning adjustments, lubrication of bearings, and impeller cleaning. Proper maintenance is crucial to prevent premature failure and maintain the efficiency of centrifugal fans.
Cost
The initial cost of EC fans is typically higher compared to centrifugal fans. The integrated design and advanced electronic components used in EC fans contribute to their higher upfront cost. However, the long-term operating costs of EC fans are often lower due to their higher efficiency, reduced maintenance requirements, and longer lifespan.
Centrifugal fans, while generally less expensive upfront, may incur higher operating costs over time. Factors such as lower efficiency, higher energy consumption, and more frequent maintenance needs can contribute to increased long-term costs.
Applications
Centrifugal fans and EC fans find applications in various industries and systems. Centrifugal fans are commonly used in HVAC systems, industrial processes, ventilation, and air pollution control. They are suitable for applications that require high airflow rates, high static pressure, and the ability to handle harsh environments.
EC fans are increasingly popular in applications that prioritize energy efficiency, precise control, and low noise. They are commonly used in air handling units, data centers, refrigeration systems, and ventilation applications where variable airflow and energy optimization are important considerations.