What is oil immersed transformer?
An oil immersed transformer, also known as an oil filled transformer, is a type of electrical transformer that uses oil as both a cooling and insulating medium. The transformer’s core and windings are submerged in a sealed tank filled with insulating oil, which serves two critical purposes: dissipating heat generated during operation and providing electrical insulation to prevent short circuits.
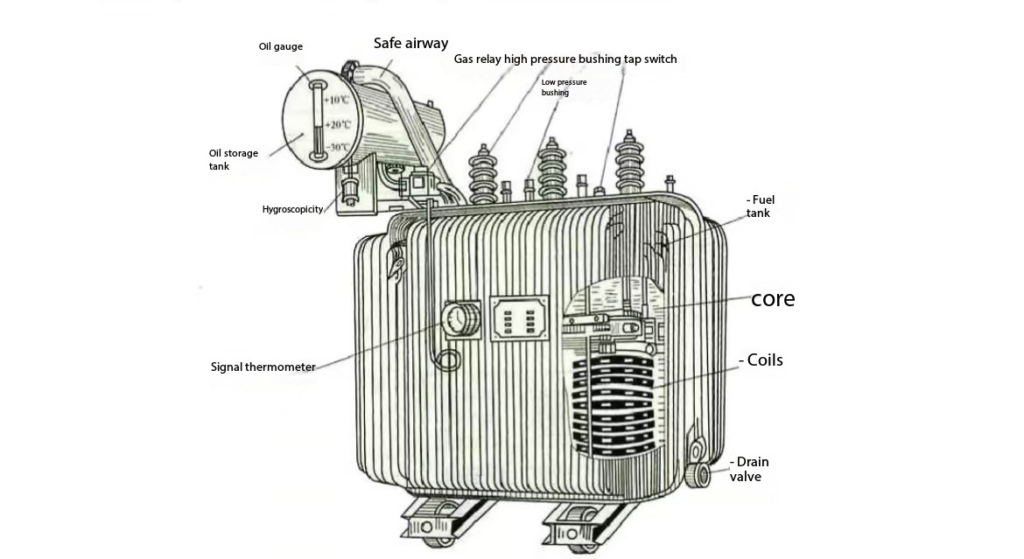
How It Works
The working principle of an oil immersed transformer revolves around electromagnetic induction. The magnetic core and windings generate heat during operation. The surrounding oil absorbs this heat and circulates through convection, transferring it to external radiators or cooling fins where it dissipates into the air. This process ensures the transformer remains at optimal operating temperatures.Additionally, the oil acts as a dielectric medium, insulating the windings and protecting them from moisture and contaminants. This dual functionality makes oil-immersed transformers highly efficient in managing large power loads.
What is a dry type transformer?
A dry type transformer is an electrical transformer that does not use any liquid (such as oil) for cooling or insulation. Instead, it relies on air or gas circulation to cool its windings and core. The windings are often encapsulated in epoxy resin or coated with varnish, providing protection against moisture, dust, and contaminants.

How It Works
Unlike oil immersed transformers, dry type transformers use natural or forced air circulation to dissipate heat. Cooling ducts within the windings allow air to flow freely, removing heat generated during operation. This simple yet effective design eliminates the need for liquid coolants while maintaining high performance.The insulation materials used in dry-type transformers (e.g., epoxy resin) are fire-resistant and environmentally friendly, making these transformers a safer option for indoor installations.
Brief introduction to the role and classification of transformer
Transformer are the backbone of modern electrical systems, enabling the efficient transfer of electrical energy between circuits through electromagnetic induction. Their primary purpose is to adjust voltage levels—either stepping them up for long-distance transmission or stepping them down for safe local distribution. Without transformers, power grids would struggle with significant energy losses, making electricity transmission inefficient and costly.
Transformers are broadly categorized based on their design and application:
- Voltage Transformation: Step-up transformer increase voltage for transmission, while step-down transformers reduce it for end-user safety. Isolation transformers, on the other hand, separate circuits for safety without altering voltage.
- Core Material: Iron core (common in high-power applications), ferrite core (used in high-frequency devices), and air core (lightweight but less efficient).
- Cooling Mechanism: Oil-immersed transformers use insulating oil, while dry-type transformers rely on air or gas.
- Application: Power transformers handle high-voltage transmission; distribution transformers manage local grids; instrument transformers aid in measurement and protection.
Basic concepts of oil immersed transformer and dry type transformer
oil immersed transformer
An oil-immersed transformer uses insulating oil to cool and insulate its components. The oil circulates within a sealed tank, dissipating heat generated during operation and protecting the windings from moisture and contaminants. These transformers are commonly found in outdoor or industrial environments.
Key Characteristics:
- Exceptional heat dissipation, making them suitable for high-power applications.
- Designed for durability but requires regular maintenance to monitor oil quality and prevent leaks.
- Commonly used in power stations, substations, and rural grids.
dry type transformer
In contrast, dry-type transformers use air or gas as a cooling medium. Their windings are often coated in epoxy resin, which protects against moisture and pollutants. These transformers are ideal for indoor environments where safety is paramount.
Key Characteristics:
- Fire-safe design since no oil is involved.
- Compact and environmentally friendly.
- Requires less maintenance but is limited to medium or low-capacity applications.
Main differences between the two transformers
The differences between oil immersed transformer and dry type transformer go beyond their cooling mechanisms—they shape their usability in diverse scenarios:
Aspect | Oil Immersed Transformer | Dry Type Transformer |
---|---|---|
Cooling Medium | Insulating oil | Air or gas |
Safety | Higher fire risk due to oil | Safer; no risk of oil-related fires |
Maintenance | Requires regular oil testing | Minimal maintenance |
Capacity | Suitable for large capacities | Limited to medium or low capacities |
Installation | Outdoor or separate transformer rooms | Indoor-friendly |
Cost | Lower initial cost | Higher initial cost |
For example, an oil-immersed transformer might power a steel plant requiring massive energy loads, while a dry-type transformer could safely operate inside a hospital where fire risks must be minimized.
Comparison of advantages and disadvantages
Feature | Oil Immersed Transformer | Dry Type Transformer |
---|---|---|
Advantages | – High capacity | – Safer for indoor use |
– Superior cooling efficiency | – Eco-friendly | |
– Cost-effective for large-scale operations | – Requires minimal upkeep | |
– Compact design | ||
Disadvantages | – Fire risk | – Higher upfront cost |
– Requires regular maintenance | – Limited capacity | |
– Environmental concerns due to oil leaks |
To illustrate: an industrial facility with heavy machinery might prioritize the cost-effectiveness of an oil-immersed transformer despite its maintenance requirements. Meanwhile, a shopping mall would likely opt for a dry-type transformer to meet safety regulations and reduce environmental impact.
dry type transformer and oil immersed transformer Application scenario analysis
Oil-Immersed Transformer
These transformers shine in:
- Power Transmission Systems: Used in high-voltage lines spanning long distances.
- Industrial Operations: Essential for factories with energy-intensive equipment like furnaces or compressors.
- Rural Power Grids: A cost-effective choice for delivering stable electricity across vast areas.
Dry-Type Transformer
These are better suited for:
- Urban Installations: Ideal for densely populated areas like skyscrapers or metro stations where fire safety is critical.
- Indoor Applications: Found in hospitals, schools, and office buildings where compactness and low noise levels are essential.
- Eco-Sensitive Zones: Preferred in areas with strict environmental regulations due to their non-toxic design.
In summary, oil-immersed transformer dominate high-power outdoor applications thanks to their efficiency and affordability. Dry-type transformer, however, excel indoors where safety, compactness, and environmental considerations take precedence. For instance, a wind farm might use an oil-immersed transformer to transmit electricity over long distances efficiently. Conversely, a residential complex would benefit from a dry-type transformer’s fire-safe design.
Choosing the right transformer boils down to understanding your needs. Ask yourself:
- Do you need high capacity? Go with an oil-immersed transformer.
- Is fire safety a top concern? Opt for dry-type.
- Are you working indoors or outdoors? Match the transformer type to your environment.
By aligning your choice with your operational priorities—whether it’s cost-efficiency, safety, or sustainability—you’ll ensure optimal performance without compromising reliability.